31. The history of StumpCraft
A history of the StumpCraft company and an introduction to its new co-designer Siri Olson (about 3400 words; 16 pictures)
Canadian-based StumpCraft has long been one of my very favourite puzzle-makers. Besides using them as the standard against which I assess other top-tier jigsaws, I have previously written review-essays about their puzzles in:
This essay is the first of a 2-part series. This part began as what turned out to be a much-too-long introduction to a review-essay so I broke it up into two separate postings. The next newsletter will be a review of the nine Canadian landscape mini-puzzles that the StumpCraft released this year and my thoughts about mini-puzzles in general.
The origins of the company
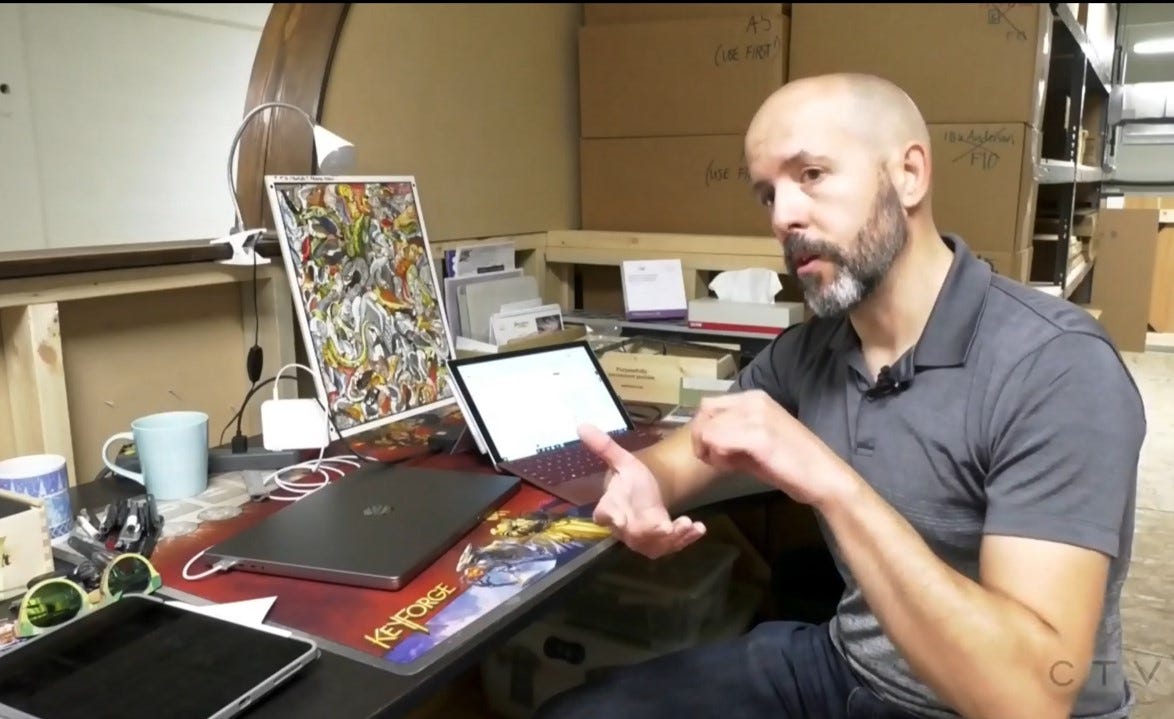
Before founding StumpCraft Jasen Robillard had much more conventional employment in Calgary, Canada’s main service centre for the oil and gas industry. He was applying his degrees in geological engineering and geophysics to managing allocation and maintenance of geological survey equipment. He also had a side-gig as a facilitator for design and development of shared facilities for condominium and cohousing developments. On his own time he was a big board-game fan – one of the founders of the Calgary Boardgame Meetup Group and an organizer and team leader for that city’s annual Fallcon Boardgame Convention.
In 2011 it was that last avocation that introduced him to the world of wooden jigsaw puzzles. Then as now, Canada had a solid presence in the world of cardboard puzzles (Cobble Hill and Eurographics are Canadian companies) but those puzzles had never held much attraction for him. But learning about the superior quality of wooden puzzles during a boardgame discussion group piqued his interest.
Canada had a few hand-cutters out East but there were no Canadian makers of laser-cut jigsaw puzzles at that time – in fact, there were only a couple of companies anywhere in the world that made them back then. (With the current abundance of laser puzzle-makers it is easy to forget that this technology only dates to the late-1990s.) So Jasen’s early wood puzzles came mostly from Liberty in Colorado and Artifact in California. Fortunately for all of us those companies make very fine puzzles. That got him hooked, and more and more of his previous boardgame time became devoted to assembling wooden jigsaw puzzles.
In early 2017, at least partly motivated by the onerous cost of shipping and importing puzzles to Canada, the avid puzzler had an eureka moment – maybe he could make them himself. He had access to laser cutting equipment through a friend as well as in local maker-space craft workshops. He was confident that his expertise with geological surveying equipment would stand him in good stead for learning the technology of laser cutting.
Jasen told me that the initial appeal for him about the idea of making puzzles himself was as a creative outlet. He was curious to see whether by applying what he had learned as an assembler he could design ones that were as good as (or better than!) those established American companies. His initial plan was for it to be a hobby/side-hustle. He aimed to be the North-of-49 equivalent to Liberty, meeting the demands of the Canadian market. He also had a not-at-all-hidden agenda of introducing people to the works of Canadian artists whose paintings he admired.
But as he began making prototypes for what was to become Summer Medley by Mandy Budan he discovered that the Chinese-made laser machines to which he had access were basically hobbyist-grade. They could not make puzzles that were of the fabrication quality to which he aspired. That led to a big decision. He needed to buy a professional-grade laser cutting machine for his basement workshop if he was to make world-class puzzles. Fortunately, his wife Heather was supportive of his dream and he acquired a top-of-the-line Trotec Speedy 300.
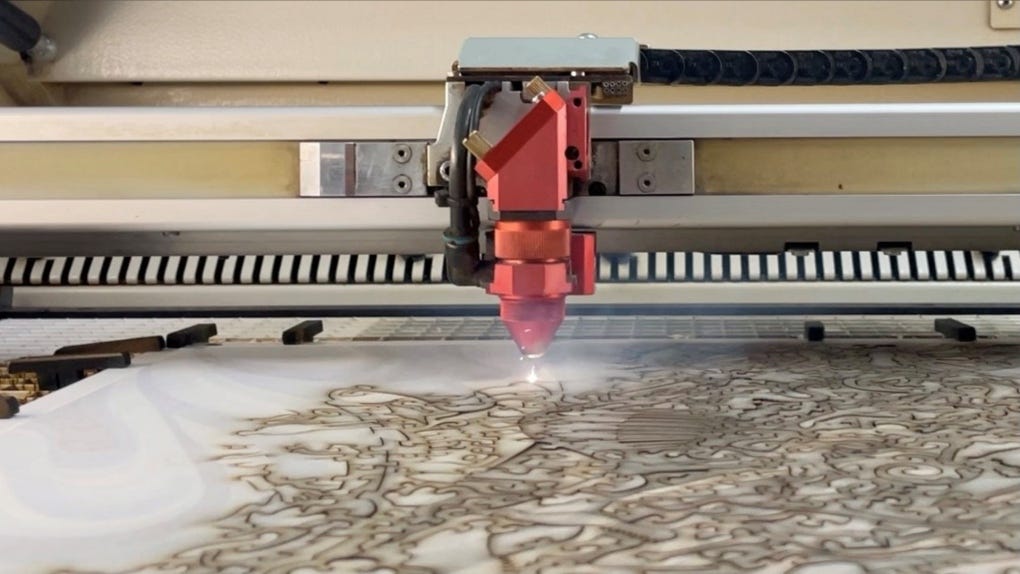
After eight months of learning how to operate the machine and resolving the inevitable teething problems, and designing four inaugural puzzles, not to mention sorting out all of the myriad details of materials-sourcing, online marketing and everything else that is involved in starting up a manufacturing business, StumpCraft was launched in September 2017.
Making superior jigsaw puzzles requires two kinds of state-of-the-art technology. The other one is printing. In my reviews (including the next one about the StumpCraft mini-puzzles) I often praise the benefits of printing directly onto the wood using a flatbed ultraviolet (UV) printer, rather than printing onto paper that is then glued down. Briefly, the printer places special ink onto the surface and then intense LED ultraviolet lights immediately polymerize the ink, drying and adhering it to the substrate. Because the microscopic dots of wet ink do not have time to soak in or spread this printing technology enables extremely fine detail.
UV inks also have a higher proportion of pigment to carrier material, enabling intense vibrant colours. The results are both waterproof and resistant to fading over time. UV printing is also more energy-efficient than conventional printing methods, and it does not out-gas the sometimes-toxic solvents found in regular ink, making it an environmentally-friendly technology. If you want to learn more, here is a good introductory article about UV printing.
But professional-grade flatbed UV printers cost as least as much as top-quality laser-cutters, and the learning curve for getting the best out of them is much steeper than learning that technology. Rather than take that on Jasen chose to have his printing done by an established local print-shop.
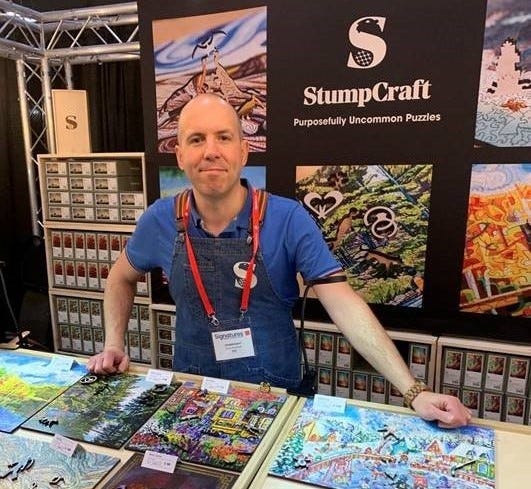
From the beginning Jasen’s primary means of selling his puzzles has been direct online marketing through his website, supplemented in the pre-Christmas season by face-to-face sales at juried craft shows in cities across Canada. Besides selling his puzzles at the shows he uses the travel to scope out new Canadian regional artists and to stay in touch with ones with whom he already has a working relationship.
The Covid pandemic brings expansion
In early 2020 the Covid pandemic hit – craft shows were cancelled but as with all jigsaw puzzle makers, cardboard or wood, online sales exploded. All around the world, high-end puzzle-makers like Liberty and Artifact had to ration their sales even to their established long-time customers. When people began to shop around online they discovered what was then this little-known Canadian company. After trying out StumpCraft they came back for more.
The huge demand for jigsaw puzzles during those first two Covid years brought another opportunity. Justin Madden, the descendant proprietor of the legendary hand-cutting puzzle-maker Par Puzzles, was also overwhelmed with orders. He tried a short-lived experiment making laser-cut ones himself but could not achieve a quality of fabrication consistent with that renowned brand. When he asked the members of the most active wooden jigsaw puzzle discussion group on Facebook to recommend top-quality puzzle cutters that he could possibly work with the name StumpCraft frequently came up. That led to three limited-edition puzzles being released under both companies’ names. You can read more about that collaboration here and in my review/essay of one of them here.
As sales grew Jasen’s side-hustle quickly turned into much more work than one person could handle. He invited two old friends to become his partners in what had become a rapidly-growing fulltime business. Cory Krygier was to be in charge of sales and James Lee would head up production. That gave Jasen more time to focus on design.
Obviously the business outgrew Jasen’s basement workshop and that led to another big decision. The partners could expand on his property for a while by converting a garage into more workshop space (it would help that Cory was a trained architect) and hope that the company could keep flying under the radar of the City’s zoning bylaws by being a “home-based business”, or they could anticipate continuing growth and move to much larger rented space in one of Calgary’s areas that is zoned for light-industry.
You can see in the following photo what the choice was:

About a year ago a reporter for the Calgary Guardian interviewed Jasen and asked him a pair of thoughtful questions:
What is the best part about what you do? What is the worst part?
By far the best part is hearing about the meaningful moments and connections that our puzzles engender in people’s lives: kids willingly turning off their cell phones and game devices to spend quality with their parents; new family traditions being made; puzzlers appreciating the themes and hidden Easter eggs I throw into each design.
For an introvert like myself, the biggest challenge is marketing within the attention economy and the negative aspects of social media. For a business that intentionally invites people to slow down, unplug and connect with art and people at the table, it’s tough to engage authentically in effective marketing that doesn’t add more noise to an already noisy world.
Jumping ahead, the company now has a loyal base of customers world-wide and makes its puzzles using three top-of-the-line laser-cutting machines. Besides Jasen, Cory and James, Siri Olson (more about her below), Steve Zanini and Nicole Ginter are now their full-time team, and even though I write this before the big pre-holidays rush has begun they have three more temporary or part-time employees on the payroll.
Cory sent me the following recent photos of StumpCraft’s workspace:


The ways that StumpCraft distributes its puzzles are also expanding. Besides their workshop store, and of course their website, to facilitate sales in the US most StumpCraft puzzles are now available through Artifact Puzzles’ website. (They are the only laser-cut puzzles that Artifact sells besides their own and their subsidiary Ecru brand.) Their puzzles are also available in selected Western Canadian gift shops and art galleries and the company is exploring other distribution opportunities.
I was surprised to learn (but perhaps I shouldn’t have been) that StumpCraft still contracts his printing to the same professional printer as when Jasen first began. As I have frequently noted in other essays, StumpCraft’s printing is the best that I have seen. Jasen has great respect for the specialized knowledge and skill his printer brings to the craft and told me that the 3D effects come from that person’s expertise and creative ability, not his own.
Besides working to build a prosperous company the StumpCraft team aims to be good corporate citizens. For example, besides actively promoting paintings by contemporary Canadian artists, they use special environmentally certified MDF (medium-density fibreboard) that is arguably more “green” than plywood (because it is comprised mainly of wood fibres that would otherwise be a waste product and is free of formaldehyde in its binding material.)
A major project for Jasen and Cory in 2024 will be working on all of the paperwork necessary to be certified as a B Corp company, internationally perhaps the most highly regarded certification attesting to exceptional environmental and corporate citizenship performance. That involves extensive documentation, not just about the company’s own practices but also about those of its suppliers. Never heard of the B Corp movement? Neither had I until I learned about it from Jasen’s blog. But you can learn more about what its certification means from this article in the Harvard Business Review.
Introducing Siri
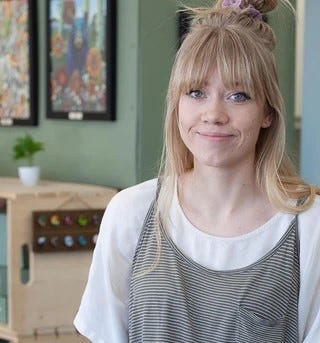
In the past year StumpCraft has been experiencing a major transition. Jasen has been training up Siri Olson to be his co-designer and the mini-puzzles that will be discussed in the next issue of this newsletter/blog are all examples of their collaboration together.
Siri comes from a creative family. Her mother is a teacher who has a natural knack for design and her father founded Leaf & Lyre, Calgary’s first urban agriculture business. Siri began working for StumpCraft after earning an 18 month graphics design diploma from the Calgary campus of the Vancouver-based Visual College of Art and Design. She graduated with their 2020 Outstanding Achievement Award for Graphic Design.
But at first she wasn’t hired by StumpCraft to be a designer – she replied to an online help-wanted ad that Jasen posted for a “seasonal de-puzzler” for the 2022 pre-Christmas rush. She told me that she was curious about what that job was. She was doing contract-based work designing text and graphics for bottles and boxes but wanted another gig that would “get her hands on 3D stuff.”
She must have been good at quality control, disassembly and packaging (which it turned out is what a “de-puzzler” does) because that temporary job turned into a full time one at Stumpcraft on the production side of things as a laser technician, and her packaging design contracts became her side-gigs.
Then one day Jasen asked her: “Would you like to try your hand at designing puzzles?” Besides her qualifications he was impressed by the artistry of her occasional doodles at work.
At first of course she was Jasen’s trainee in that role, learning the craft and following his instructions in helping to fine-tune his cutting designs. But before long Jasen began to give her the role of creating the first draft of cutting patterns, with both of them participating in refining the designs. As I understand it, from both Jasen and Siri in separate interviews, collaboration is now much less like a trainee relationship and already more resembles them being co-designers but with Jasen’s greater experience giving him something more like a mentor role. They comment and make suggestions about each other’s cutting patterns while the designs are still in development, but now pretty much work independently on their separate projects.
In the Calgary Artists series of mini-puzzles, that will be reviewed in my next essay, Siri is given sole credit as the designer for Larch Valley (although she told me that she did get some help from Jasen) while Jasen is shown as the designer of the other two (although Siri also contributed some suggestions and assistance.) I understand that the main difference is really in who designed the first draft. In all of the Reilly Fitzgerald and Catherine Robertson mini-puzzles puzzles both designers are credited but with Siri usually getting first billing. She is also listed as the co-designer of the two cutting patterns for their custom-made puzzles.
StumpCraft’s house style is for their figurals to be silhouettes, without relying on additional accent lines that help bring the whimsy to life but also can detract from appreciation of the puzzle image. It is tougher to make recognizable figures that way but Jasen is a master at lifelike silhouettes and obviously so is Siri. The following photo shows whimsies from mini-puzzles for which Siri is given top billing as the designer.
The first larger puzzle for which Siri is credited as the primary designer was the 200 piece Lac La Hache Wildflowers by Lori Anne McKague, which also credits the artist, Lori Anne McKague, and Jasen as design collaborators. I especially like the way that the owl multi-piece whimsy gets its eyes from wildflowers in the image.

In the StumpCraft “Deep Dive” blog post about Lac La Hache Wildflowers Siri describes how she feels about designing:
As a creative person, my work doesn’t feel complete until I make clever things. I like the art I craft to provoke deeper thought, to have the subtle layered underneath the obvious. From a young age, I have always been inspired by unnoticed things, the details that most people pass by. Maybe it’s because I’m a quiet person, but small and silent things hold my interest.
Sometimes art feels too loud, too much for my brain. Art often overwhelms me by the sheer scope of its possibilities. Design on the other hand feels more constrained and is actually the domain where I come alive. The fact that design has a destination—a target audience and outcomes—guides the process of creating for me.
Those design parameters form the boundaries of the box that I then work to think outside of. Kudos to the artists who embrace that vulnerable, boxless unknown.
Over the past Spring and Summer, Siri’s job has primarily been as a designer but with periodic breaks to tend one of the machines. That involves reacting to a timer that she sets – 47 to 52 minutes depending on what is being cut. That tells her it is time to remove the newly made puzzle from the laser cutter, do a quick quality control check and adjust the machine if needed, then line up a new board for it to cut. She says that takes about 5 minutes and then it’s back to designing. She told me that sometimes she resents the intrusion into her focus, but mostly it is a welcome reminder of the need for a stretch-break.
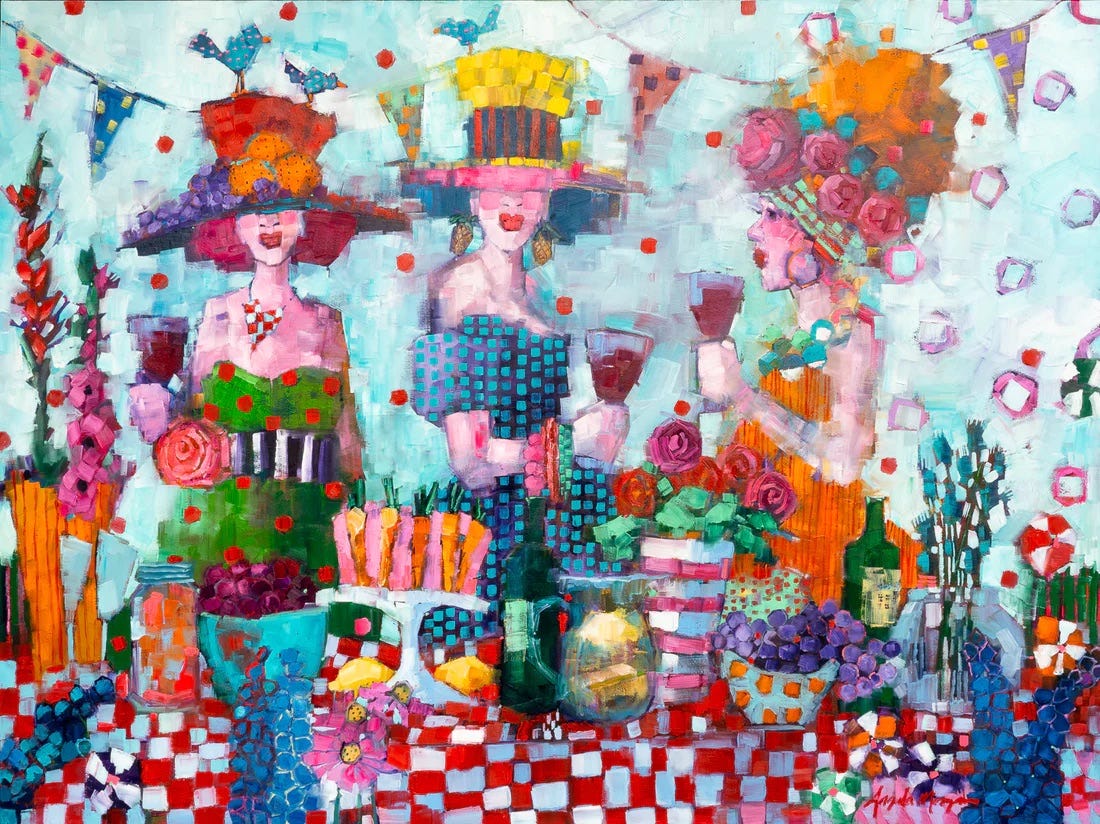
StumpCraft has just released Siri’s first design for a really large puzzle – about 562 pieces. It is the recently-released not easily phased by Angela Morgan. She told me that designing it was a lot of fun, and her design notes in the puzzle’s Deep Dive essay show that a lot of thought went into the whimsies and whimwhams. For example, the puzzle includes three multi-piece whimsies that are like dress-up dolls, each with three possible dresses.
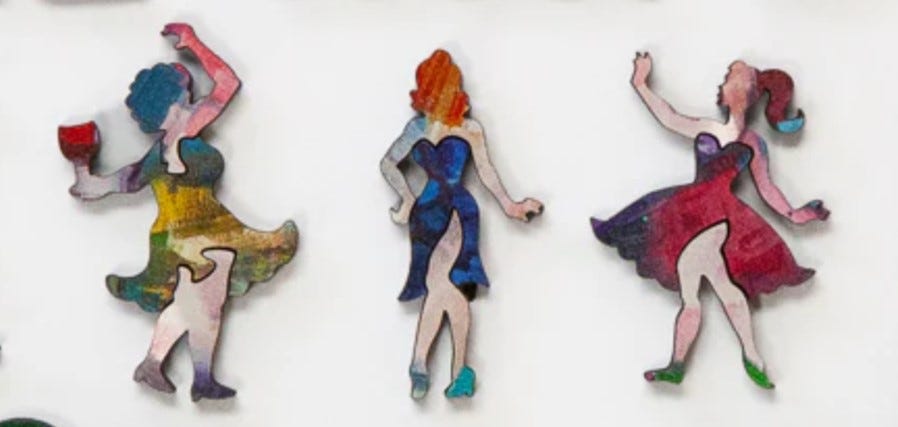
I understand that she and Jasen discussed ideas and concepts during the initial design phase, but after that she worked pretty much independently on it. This puzzle is not for those who are easily phased: StumpCraft has given it a rare 5 out of 5 difficulty rating and even their 888 piece We Are the Lotus Kids gets only 4 out of 5. (In parallel to Siri working on this one, Jasen has been working on a challenging line-cut pattern for the long-awaited Feline Tessellation by Cedarfell, the release of which is now postponed until early next year.)
As with all wood puzzle companies, the seasonal cycle is especially pronounced. I already knew about this being a busy season but was surprised to hear from Cory that that October to December accounts for a significant majority of Stumpcraft’s all of their annual sales! It is not just because jigsaw puzzle assembly is especially suitable for wintertime or because of the pre-Christmas craft shows. Due to their price, high quality wood puzzles are a special treat, and a high proportion of wood puzzles are sold to be holiday season gifts or as personal holiday splurges. That busy season is beginning about now.
According to mid-September correspondence from Jasen:
The puzzle season has ebbs and flows. From January to Aug my focus is on design and long term planning, and from Sept to Dec my work generally is more tactical and logistics related to our craft markets. Siri's schedule follows a similar rhythm. Once her next design is complete (next week?) Siri will be helping out more with production once again. Even I occasionally step into laser cutting, de-puzzling, and order fulfillment as the need arises (like for example this weekend).
So for the next few months Siri will primarily be back to being a laser technician and disassembler, but she will also have a few opportunities to meet the public at craft shows. But I’m sure that Siri is already coming up with creative cutting ideas for whatever design projects she will be taking on after the big seasonal rush is over.

Dear Bill.
I'd have replied sooner to this fine post if I hadn't felt rather harried over the past too weeks.
I enjoyed reading about Jasen Robillard's career arc. Isn't life puzzling?!
I didn't know anything about how UV and intense LED lighting had anything to do with superior inking of colour onto puzzle pieces! That was very interesting, too.
I did know that the Covid-19 pandemic had a lot to do with people getting more occupied with indoor activities.
Good on you for introducing the StumpCraft team. I'm pleased to know that they care about being good (and environmentally caring) citizens.
Of the glimpses of puzzles we got today, I like "Not Easily Phased" best.
I'm looking forward to learning about and, I hope, seeing StumpCraft landscape puzzles in your next post.
Best regards,
Greg
Thanks Bill - excellent writing as always. Clearly, you can make any topic interesting!